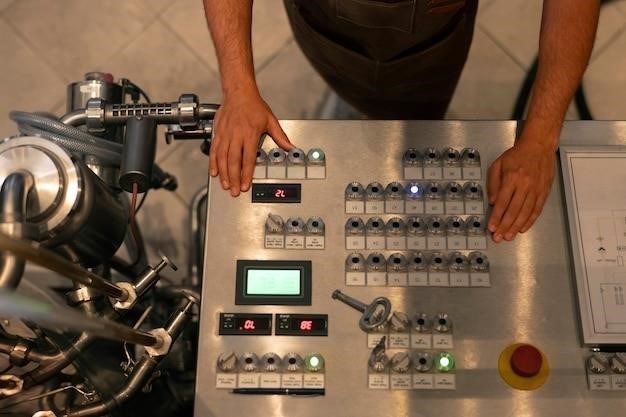
Tennant T7 Troubleshooting Manual⁚ A Comprehensive Guide
This manual provides service information for the TENNANT Model T7. This machine will provide excellent service. However, the best results will be obtained at …
Introduction
The Tennant T7 is a powerful and versatile floor scrubber designed for cleaning a variety of surfaces. This troubleshooting manual is a comprehensive guide to help you identify and resolve common issues that may arise during the operation of your T7 machine. It provides detailed instructions and troubleshooting tips for various problems, from basic maintenance to more complex technical issues.
Whether you are a seasoned operator or a novice user, this manual will equip you with the knowledge and skills to keep your T7 machine running smoothly and efficiently. It will guide you through the process of diagnosing problems, understanding fault codes, and performing necessary repairs.
Identifying the Problem
Before attempting any troubleshooting, it’s crucial to accurately identify the problem with your Tennant T7. Begin by carefully observing the machine’s behavior. Does it make unusual noises? Are there any warning lights illuminated on the dashboard? Are specific functions not working as intended? Take note of any error messages displayed on the control panel.
Once you’ve identified the problem, consult this troubleshooting manual for specific instructions and solutions. The manual provides detailed descriptions of common issues, their potential causes, and recommended actions to resolve them. By systematically examining the machine and its symptoms, you can effectively pinpoint the root cause of the problem and proceed with appropriate troubleshooting steps.
Troubleshooting Common Issues
The Tennant T7 is a robust machine, but like any equipment, it can encounter occasional issues. This section covers some of the most common problems and provides solutions. If you experience trailing water, poor or no water pickup, check if the vacuum fan is turned off or if the squeegee blades are worn. If the vacuum fan is not turning on, ensure the fan motor is properly connected and receives power. For little or no solution flow, inspect the solution supply lines for blockages.
Poor scrubbing performance might indicate a clogged scrub brush or worn-out pads. Lastly, if the One Step Scrub button is not working, verify its connection and power supply. Remember, this section provides a general overview of common issues. For more detailed troubleshooting steps and solutions, consult the specific sections within this manual.
Trailing Water ⎼ Poor or No Water Pickup
Trailing water or poor water pickup can be a frustrating issue. Here are the common culprits and how to address them⁚
- Vacuum Fan Turned Off⁚ Double-check that the vacuum fan is turned on. A simple oversight can cause this problem.
- Worn Squeegee Blades⁚ Over time, squeegee blades wear down, reducing their effectiveness. Inspect the blades for wear and tear, and replace them if necessary.
- Squeegee Out of Alignment⁚ If the squeegee is misaligned, it won’t properly pick up water. Adjust the squeegee to ensure it sits flush against the floor.
- Clogged Vacuum Motor Filter⁚ A clogged filter can restrict airflow, impacting water pickup. Clean or replace the filter as needed.
By addressing these common causes, you can usually resolve trailing water issues and ensure efficient floor cleaning.
Vacuum Fan Not Turning On
A vacuum fan that won’t turn on is a major problem, preventing proper water pickup and leaving floors wet. Here’s a breakdown of the potential issues and how to troubleshoot them⁚
- Vacuum Fan Fuse Blown⁚ Check the vacuum fan fuse for signs of damage or a blown fuse. Replace it if necessary.
- Vacuum Fan Motor Malfunction⁚ If the fuse is intact, the problem might lie with the vacuum fan motor itself. Inspect the motor for damage or signs of overheating. A faulty motor will need to be replaced.
- Vacuum Fan Switch Problem⁚ The vacuum fan switch may be faulty, preventing power from reaching the motor. Test the switch and replace it if it’s not functioning properly.
- Wiring Issues⁚ Check for loose or damaged wiring connecting the vacuum fan to the control panel. Repair or replace any faulty wiring.
Remember to always consult the Tennant T7 service manual for specific instructions and diagrams related to your model.
Little or No Solution Flow to the Floor
If you’re experiencing a lack of solution flow to the floor during scrubbing, it could be due to a few common causes. Here’s a guide to troubleshooting these issues⁚
- Solution Tank Empty⁚ The most obvious reason for no solution flow is an empty solution tank. Check the tank level and refill it as needed.
- Solution Pump Malfunction⁚ The solution pump might be faulty, preventing solution from being delivered to the floor. Inspect the pump for damage or signs of malfunction. If the pump is faulty, it will need to be replaced.
- Solution Lines Clogged⁚ The solution lines connecting the tank to the scrub head can become clogged with debris or chemicals. Inspect and clean these lines to ensure proper flow.
- Solution Flow Control Valve Issue⁚ The solution flow control valve might be stuck closed or malfunctioning. Check the valve and adjust or replace it if necessary.
- Solution Level Sensor Problem⁚ A faulty solution level sensor can prevent the machine from detecting an empty tank, leading to a lack of solution flow. Check and clean the sensor, or replace it if needed.
Remember to consult the Tennant T7 service manual for specific instructions and diagrams related to your model.
Poor Scrubbing Performance
If your Tennant T7 isn’t scrubbing effectively, it could be a sign of several potential issues. Here’s a breakdown of common causes and how to address them⁚
- Worn Scrub Brushes⁚ Over time, scrub brushes wear down and lose their effectiveness. Inspect the brushes for signs of wear, and replace them if they are worn or damaged.
- Incorrect Brush Pressure⁚ The brush pressure needs to be adjusted to match the type of floor you’re cleaning. Check the pressure settings and adjust them as needed. Refer to the Tennant T7 service manual for specific instructions.
- Clogged Brush Head⁚ Debris and dirt can accumulate in the brush head, hindering cleaning performance. Remove the brush head and thoroughly clean it to remove any obstructions.
- Insufficient Solution Flow⁚ If the solution flow is insufficient, it can impact scrubbing effectiveness. Check the solution flow and address any issues that may be preventing proper delivery.
- Squeegee Blade Issues⁚ Worn or misaligned squeegee blades can leave streaks or residue on the floor. Inspect the blades and replace them if necessary. Ensure the blades are properly aligned for optimal performance.
Addressing these common issues can significantly improve the scrubbing performance of your Tennant T7. Always refer to the service manual for detailed instructions and specifications specific to your machine.
One Step Scrub Button Not On
The “One Step Scrub” button on your Tennant T7 provides a convenient way to activate both the scrub brush and the solution flow simultaneously. If this button isn’t working, it can significantly hinder your cleaning efficiency. Here’s a breakdown of potential causes and solutions⁚
- Button Malfunction⁚ The button itself could be faulty. Inspect the button for any visible damage or signs of wear. If the button appears damaged, it may need to be replaced.
- Electrical Connection Issues⁚ A loose connection in the wiring leading to the button can prevent it from functioning properly. Carefully inspect the wiring for any loose connections or signs of damage. Reconnect any loose wires or replace damaged wires.
- Control Panel Malfunction⁚ The control panel itself could be faulty, impacting the functionality of the “One Step Scrub” button. If other buttons on the control panel are also unresponsive, the control panel may need to be repaired or replaced.
- Software Glitch⁚ In some cases, a software glitch could be interfering with the button’s functionality. Check if there are any software updates available for your Tennant T7. If so, update the software to see if it resolves the issue.
If you’ve checked these potential causes and the “One Step Scrub” button still isn’t working, it’s recommended to contact Tennant support for further assistance.
Advanced Troubleshooting
Advanced troubleshooting for the Tennant T7 requires a deeper understanding of the machine’s electrical and mechanical systems; This section will guide you through diagnosing and resolving complex issues that may require specialized tools and knowledge.
Before attempting any advanced troubleshooting, ensure you have consulted the Tennant T7 service manual for detailed instructions and diagrams.
If you are not comfortable performing advanced troubleshooting procedures, it is strongly recommended to contact a qualified Tennant technician.
Here are some key areas to consider for advanced troubleshooting⁚
- Electrical System⁚ Check for faulty wiring, blown fuses, or malfunctioning electrical components. Use a multimeter to test voltage and current readings.
- Hydraulic System⁚ Investigate potential leaks, blockages, or issues with the hydraulic pump or motor.
- Control System⁚ Diagnose problems with the control panel, sensors, or software.
Remember, safety is paramount. Always disconnect the power supply before working on the electrical system and use appropriate safety precautions when working with hydraulic systems.
High Current Faults
High current faults are a common issue in the Tennant T7, often indicating a problem with the machine’s electrical system. These faults can trigger alarm codes and lead to the machine stopping.
The most common cause of high current faults is a faulty motor or control module. However, other issues like faulty wiring, shorted circuits, or overloaded components can also cause high current faults.
Here’s how to troubleshoot high current faults⁚
- Check the alarm codes⁚ The Tennant T7 will display alarm codes on the control panel to indicate the type of fault. Refer to the service manual to understand the meaning of each alarm code.
- Inspect the motor and control module⁚ Examine the motor and control module for signs of damage, overheating, or loose connections.
- Test the electrical system⁚ Use a multimeter to check for continuity in wiring and to measure voltage and current readings.
- Verify proper grounding⁚ Ensure that the machine is properly grounded to prevent electrical shocks.
If you are unable to identify the cause of the high current fault, it is essential to contact a qualified Tennant technician for assistance.
Propel System Troubleshooting
The propel system of the Tennant T7 is responsible for the machine’s forward and reverse movement. If the propel system malfunctions, the machine will not move, or it may move erratically. Here are some common propel system issues and their solutions⁚
- No movement⁚ Check the propel motor for damage, loose connections, or a blown fuse. Ensure the propel system is engaged and that the control lever is functioning properly.
- Erratic movement⁚ Inspect the propel system for any loose or damaged parts, including the drive belts, sprockets, and wheels. Check the propel motor for signs of overheating or binding.
- Uneven movement⁚ Verify that the propel motor is receiving adequate power. Check the battery connections and ensure the battery is fully charged.
- Propel system alarm⁚ The Tennant T7 will sound an alarm if it detects a propel system fault. Refer to the alarm code chart in the service manual for troubleshooting information.
If you are unable to resolve the issue, it is recommended to contact a qualified Tennant technician for further diagnosis and repair.
Maintenance and Repair
Regular maintenance is crucial for ensuring optimal performance and longevity of your Tennant T7. Here are some key maintenance tasks that should be performed periodically⁚
- Check and adjust belt tension⁚ Ensure proper belt tension every 100 hours of operation to prevent slippage and premature wear. A deflection of 6 mm (0.25 in) from a force of 2.3 to 2.5 kg (5.0 to 5.4 lb) at the belt midpoint is recommended.
- Clean and inspect the squeegee blades⁚ Worn or damaged squeegee blades can affect cleaning efficiency and leave streaks on the floor. Replace blades as needed and regularly clean them to remove debris.
- Clean and inspect the scrub brush⁚ The scrub brush should be cleaned and inspected regularly to remove debris and ensure optimal scrubbing performance. Replace the brush when worn or damaged.
- Inspect and clean the solution tank⁚ Regularly clean the solution tank to prevent build-up of residue and ensure proper solution flow.
- Inspect and clean the recovery tank⁚ Clean the recovery tank to prevent clogging and ensure proper suction. Remove and rinse the screen/cylinder filter located at the bottom of the tank regularly.
- Check and replace filters⁚ Regularly check and replace filters, such as the air filter, solution filter, and recovery filter, to maintain optimal machine operation and prevent damage to internal components.
It is recommended to refer to the Tennant T7 service manual for specific maintenance procedures and intervals.
Replacing Parts
Replacing worn or damaged parts is essential for maintaining the optimal performance and safety of your Tennant T7. When replacing parts, always use genuine Tennant parts or approved equivalents. Using non-approved parts can lead to performance issues, safety hazards, and void your warranty.
Here are some common parts that may need replacement⁚
- Squeegee blades⁚ Worn or damaged squeegee blades can lead to poor water pickup and streaking. Replace them as needed.
- Scrub brushes⁚ Worn or damaged scrub brushes can reduce cleaning effectiveness. Replace them when they show signs of wear or damage.
- Filters⁚ Filters, such as the air filter, solution filter, and recovery filter, should be replaced according to the manufacturer’s recommendations or when they become clogged or damaged.
- Belts⁚ Belts can wear out over time. Inspect them regularly and replace them if they show signs of wear or damage;
- Batteries⁚ Batteries eventually lose their capacity. Replace them when they can no longer hold a sufficient charge.
Refer to the Tennant T7 service manual for detailed instructions on replacing specific parts.
Adjusting Squeegee Deflection
Proper squeegee deflection is crucial for effective water pickup and a clean, streak-free floor. The deflection should be adjusted based on the type of flooring being cleaned. For smooth floors, a deflection of 12 mm (0;50 in) is typically recommended, while for rough floors, a deflection of 15 mm (0.62 in) may be necessary.
To adjust the squeegee deflection, follow these steps⁚
- Locate the adjustment knob on the squeegee assembly.
- Use a wrench or screwdriver to turn the knob clockwise to increase deflection or counterclockwise to decrease deflection.
- Check the deflection by pressing down on the squeegee blade and measuring the distance between the blade and the floor.
- Adjust the deflection as needed until it meets the recommended setting for your floor type.
Regularly check and adjust the squeegee deflection to ensure optimal cleaning performance.