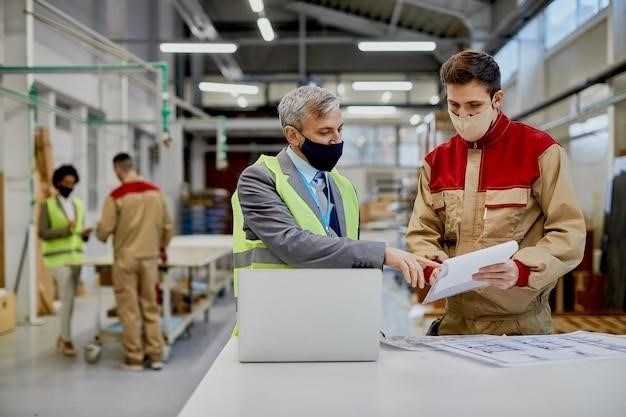
Work Instructions for Production⁚ A Comprehensive Guide
Work instructions are essential documents in any production environment. They provide detailed guidance on how to perform specific tasks, ensuring consistency, accuracy, and efficiency. This comprehensive guide will explore the importance, components, benefits, and best practices for creating and using work instructions in production settings. From defining what work instructions are to exploring visual work instructions and integration into production processes, we will cover all aspects of this crucial aspect of manufacturing.
What are Work Instructions?
Work instructions, often referred to as WIs, are detailed, step-by-step guides that outline how to perform a specific task or activity within a production process. They serve as a reference point for employees, ensuring consistency and accuracy in the execution of tasks. Work instructions are not merely procedural guidelines; they are the living record of best practices at the time, capturing the most efficient and effective methods for completing a particular task.
Imagine a symphony orchestra⁚ each musician relies on sheet music to play their part in harmony. Similarly, in a production setting, work instructions provide the “sheet music” for employees, guiding them through the intricate steps of their assigned tasks. These instructions break down complex processes into manageable, sequential steps, ensuring clarity and minimizing the risk of errors.
In essence, work instructions act as a bridge between the overall production process and the specific tasks that contribute to it. While processes define the overall flow of activities, and procedures outline the sequence of actions and responsibilities, work instructions delve into the granular details of task execution. They provide clear, concise instructions, eliminating ambiguity and ensuring that every step is completed correctly and efficiently.
The Importance of Work Instructions
Work instructions are not merely optional documents; they are the cornerstone of a well-organized and efficient production process. Their importance cannot be overstated, as they play a crucial role in achieving consistent quality, maximizing productivity, and minimizing errors.
One of the primary benefits of work instructions is their ability to standardize processes, ensuring that tasks are performed consistently across the board. This consistency translates directly into product quality, as every step is executed with the same precision and adherence to standards. By eliminating variations in how tasks are performed, work instructions minimize the risk of defects and ensure that products meet the required specifications every time.
Furthermore, work instructions streamline operations, reducing the time and effort required to complete tasks. By providing clear, concise instructions, they eliminate the need for constant supervision and reduce the likelihood of mistakes. This streamlined workflow allows employees to focus on their tasks, maximizing their productivity and efficiency.
Beyond their impact on production efficiency, work instructions also serve as a valuable tool for training new employees. They provide a clear and comprehensive guide to the tasks they need to perform, facilitating a smooth onboarding process and ensuring that new hires are quickly integrated into the production workflow. Well-written work instructions can significantly reduce the time it takes for new employees to become productive members of the team.
Key Components of a Work Instruction Template
A well-structured work instruction template is essential for creating effective and comprehensive work instructions. It provides a standardized framework that ensures consistency and clarity across all instructions, making them easy to understand and follow. Here are the key components typically included in a work instruction template⁚
- Title and Revision Number⁚ A clear and concise title that accurately reflects the content of the instruction. The revision number ensures that everyone is using the latest version of the document.
- Purpose⁚ Briefly explains the objective of the work instruction and the overall goal of the task being described.
- Scope⁚ Defines the boundaries of the work instruction, outlining the specific tasks, equipment, and materials covered.
- References⁚ Lists any relevant documents, standards, or procedures that should be consulted for additional information.
- Responsibilities⁚ Clearly defines the roles and responsibilities of individuals involved in the task, ensuring that everyone understands their role and accountability.
- Procedure⁚ The heart of the work instruction, this section provides a detailed step-by-step guide on how to perform the task. It should be written in a clear, concise, and logical manner, using visuals and diagrams when necessary.
- Safety Precautions⁚ Highlights any safety hazards associated with the task and outlines the necessary precautions to ensure the well-being of employees.
- Quality Control⁚ Outlines the quality checks and inspections that should be conducted throughout the task to ensure that the work meets the required standards.
- Record Keeping⁚ Specifies the records that should be maintained, including date, time, and any deviations from the standard procedure.
- Review and Approval⁚ Includes spaces for the names and dates of the individuals who reviewed and approved the work instruction, ensuring accountability and quality control.
By incorporating these key components, work instruction templates provide a robust framework for creating clear, concise, and effective instructions that enhance efficiency and consistency in production processes.
Benefits of Using Work Instruction Templates
Work instruction templates offer numerous benefits for organizations seeking to improve efficiency, consistency, and quality within their production processes. By standardizing the creation and implementation of work instructions, these templates streamline operations and ensure that everyone is on the same page. Here are some key advantages of using work instruction templates⁚
- Enhanced Consistency and Accuracy⁚ Templates ensure that all work instructions adhere to a standardized format, reducing the risk of errors and inconsistencies. This consistency leads to more accurate and reliable production processes.
- Improved Training and Onboarding⁚ Templates provide a clear and structured guide for training new employees, helping them quickly understand the tasks and procedures involved in their roles. This accelerates the onboarding process and reduces the time required for new hires to become productive members of the team.
- Reduced Errors and Waste⁚ By providing detailed instructions and checklists, templates help minimize errors, rework, and waste. This leads to cost savings and improved productivity.
- Enhanced Communication and Collaboration⁚ Templates foster clear communication between departments and individuals involved in production processes. Everyone understands the expectations, responsibilities, and procedures, fostering seamless collaboration and reducing misunderstandings.
- Improved Quality Control⁚ Templates incorporate quality control measures, ensuring that products and processes meet the required standards. This helps organizations maintain consistent quality and reduce customer complaints.
- Streamlined Documentation⁚ Templates streamline the creation and management of work instructions, making it easier to create, update, and store documents. This saves time and effort, improving overall efficiency.
- Increased Efficiency and Productivity⁚ By reducing errors, streamlining processes, and improving communication, work instruction templates ultimately lead to increased efficiency and productivity throughout the production process.
Work instruction templates are a valuable tool for organizations seeking to improve their production processes and achieve greater success. By utilizing these templates, businesses can create a more efficient, consistent, and reliable production environment.
Types of Work Instruction Templates
Work instruction templates come in various forms, each designed to cater to specific needs and industries. The choice of template depends on the complexity of the task, the target audience, and the preferred style of communication. Here are some common types of work instruction templates⁚
- Standard Operating Procedures (SOPs)⁚ SOPs are comprehensive documents that outline the standard procedures for a particular task or process. They are typically used for complex processes that require detailed instructions and multiple steps. SOPs are often used in regulated industries like healthcare and pharmaceuticals.
- Job Instructions⁚ Job instructions are more focused on specific tasks and are designed to be easily understood by individual workers. They often include step-by-step instructions, visual aids, and checklists.
- Visual Work Instructions⁚ These templates heavily rely on images, diagrams, and videos to illustrate procedures. They are particularly helpful for tasks that involve complex assembly, troubleshooting, or safety procedures. Visual work instructions are often used in manufacturing and engineering industries.
- Interactive Work Instructions⁚ Interactive templates allow users to interact with the instructions, such as clicking on buttons or entering data. This can help to make the instructions more engaging and improve comprehension. Interactive work instructions are often used for training and onboarding purposes.
- Digital Work Instructions⁚ These templates are created and stored electronically, making them easily accessible and searchable. They can be integrated with other systems, such as enterprise resource planning (ERP) software or learning management systems (LMS).
The choice of template depends on the specific requirements of the task or process. By selecting the appropriate template, organizations can ensure that their work instructions are clear, concise, and effective in conveying the necessary information.
Creating Effective Work Instructions
Developing effective work instructions is crucial for ensuring consistent quality and efficiency in production. Here are some key principles to consider when creating work instructions⁚
- Clarity and Conciseness⁚ Work instructions should be written in clear, concise language that is easy to understand for all employees. Avoid jargon and technical terms that may not be familiar to everyone.
- Step-by-Step Instructions⁚ Break down the task into sequential steps, providing detailed instructions for each step. This helps ensure that employees follow the correct procedure.
- Visual Aids⁚ Incorporate visual aids, such as images, diagrams, or videos, to enhance comprehension and make the instructions more engaging. Visuals can be especially helpful for complex tasks or those involving physical processes.
- Consistency and Standardization⁚ Use a consistent format and style for all work instructions. This helps to make them easily recognizable and navigate. Standardize the use of headings, subheadings, bullet points, and other formatting elements.
- Review and Approval⁚ Ensure that work instructions are reviewed and approved by relevant stakeholders, including subject matter experts, supervisors, and safety personnel. This helps to ensure that the instructions are accurate, complete, and meet all safety standards.
- Regular Updates⁚ Work instructions should be reviewed and updated regularly to reflect any changes in processes, procedures, or technology. This ensures that the instructions remain current and relevant.
By following these principles, organizations can create effective work instructions that empower employees, improve quality, and enhance productivity in the production environment.
Visual Work Instructions
Visual work instructions are a powerful tool for enhancing comprehension and retention in production environments. They go beyond traditional text-based instructions by incorporating images, diagrams, videos, and other visual elements to illustrate processes and procedures. This approach offers numerous benefits, including⁚
- Increased Comprehension⁚ Visuals can convey complex information more effectively than text alone, especially for tasks involving physical processes or intricate steps. They make it easier for employees to understand the sequence of actions, the use of tools, and the desired outcomes.
- Reduced Errors⁚ Clear visuals can significantly reduce errors by providing a clear visual representation of the correct process. They can also highlight potential hazards or areas of caution, minimizing safety risks.
- Improved Training and Onboarding⁚ Visual work instructions are particularly beneficial for training new employees. They provide a visual reference point for learning and can accelerate the onboarding process.
- Enhanced Engagement⁚ Visuals can make work instructions more engaging and appealing to employees, increasing their motivation and interest in learning the procedures.
- Language Independence⁚ Visual work instructions can overcome language barriers, making them accessible to employees who may not speak the primary language of the workplace.
When incorporating visuals into work instructions, it’s essential to choose appropriate images and diagrams, use clear and concise labels, and ensure that the visual elements are well-integrated with the written instructions. By incorporating these elements, organizations can create engaging and effective visual work instructions that enhance efficiency, reduce errors, and improve overall production outcomes.
Using Work Instructions for New Employees
Work instructions play a crucial role in onboarding new employees and ensuring a smooth transition into the production environment. A well-structured and comprehensive set of work instructions can provide new hires with the necessary information and guidance to perform their tasks effectively and safely. Here’s how work instructions can be utilized for new employees⁚
- Training and Onboarding Resource⁚ Work instructions can serve as a valuable training resource for new employees. They can be used to introduce them to specific tasks, procedures, and safety protocols, providing a comprehensive overview of their responsibilities.
- Reference Guide⁚ Work instructions provide a readily accessible reference guide for new employees. They can refer to the instructions whenever they need clarification or a refresher on a particular task.
- Consistency and Standardization⁚ Work instructions ensure that all new employees receive the same training and follow standardized procedures, contributing to consistency across the production process.
- Reduced Errors and Improved Safety⁚ By providing clear and detailed instructions, work instructions can help reduce errors and improve safety among new employees. They can highlight potential hazards, safety precautions, and proper handling procedures.
- Confidence Building⁚ Clear and well-organized work instructions can boost the confidence of new employees by giving them the tools and information they need to succeed in their roles.
When using work instructions for new employees, it’s important to ensure they are accessible, easy to understand, and tailored to the specific needs of the new hires. Consider providing additional support, such as hands-on training or mentorship, to help new employees fully grasp the information and apply it in their daily work.
Integrating Work Instructions into Production Processes
Integrating work instructions seamlessly into production processes is crucial for maximizing efficiency, minimizing errors, and ensuring consistent product quality. Here are key strategies for effectively integrating work instructions⁚
- Accessibility and Availability⁚ Make work instructions easily accessible to all employees involved in the production process. This could involve storing them in a centralized location, using digital platforms, or providing printed copies at workstations. Ensure that instructions are readily available whenever and wherever they are needed.
- Clear Labeling and Organization⁚ Label and organize work instructions clearly to facilitate quick and easy identification. Use a consistent naming convention and organize them by task, product, or production line. This allows employees to locate the specific instructions they need without delay.
- Training and Familiarization⁚ Provide comprehensive training to all employees on how to use work instructions effectively. This training should cover locating instructions, understanding the format, and applying the information to their tasks. Regular refresher courses or updates can help ensure employees stay familiar with the latest versions of instructions.
- Feedback and Revision⁚ Encourage employees to provide feedback on the effectiveness of work instructions. Regularly review and revise instructions based on feedback, observations, and changes in production processes. This iterative process ensures that instructions remain current and relevant.
- Technology Integration⁚ Explore the use of digital tools and technologies to streamline the integration of work instructions. Digital platforms can facilitate online access, version control, updates, and even real-time tracking of instruction usage. This can enhance efficiency and reduce the risk of outdated or inaccurate information.
By integrating work instructions effectively, organizations can create a more efficient, consistent, and safe production environment. The use of digital tools and technologies can further enhance this integration, paving the way for a more streamlined and responsive production process.
Best Practices for Writing Work Instructions
Crafting clear, concise, and effective work instructions is crucial for ensuring accuracy, efficiency, and safety in production processes. Here are some best practices to follow when writing work instructions⁚
- Define the Scope⁚ Clearly define the scope of the work instruction, specifying the task or process it covers. This helps ensure that employees understand the specific activity being addressed.
- Use Simple Language⁚ Employ clear and concise language that is easily understood by all employees, regardless of their technical background. Avoid jargon or complex terminology.
- Provide Step-by-Step Instructions⁚ Outline the steps involved in the task in a logical sequence. Use clear and concise language to describe each step, ensuring that employees can easily follow the instructions.
- Include Visual Aids⁚ Incorporate visual aids such as diagrams, illustrations, or photographs to complement written instructions. This can enhance comprehension and make the instructions more engaging.
- Specify Materials and Tools⁚ List the required materials and tools for the task, including quantities and specifications. This ensures that employees have everything they need to complete the task successfully.
- Address Safety Precautions⁚ Highlight safety precautions that should be taken while performing the task. This helps ensure the safety of employees and prevents accidents.
- Review and Revise⁚ Have the work instructions reviewed by colleagues, supervisors, or subject matter experts. Solicit feedback and revise the instructions as needed to ensure accuracy, clarity, and comprehensiveness.
By adhering to these best practices, organizations can create work instructions that are effective, clear, and easy to follow, leading to improved production efficiency and quality.